PROFESSIONAL LASER WELDING SERVICES FOR PRECISION APPLICATIONS
State of the Art Welding Equipment
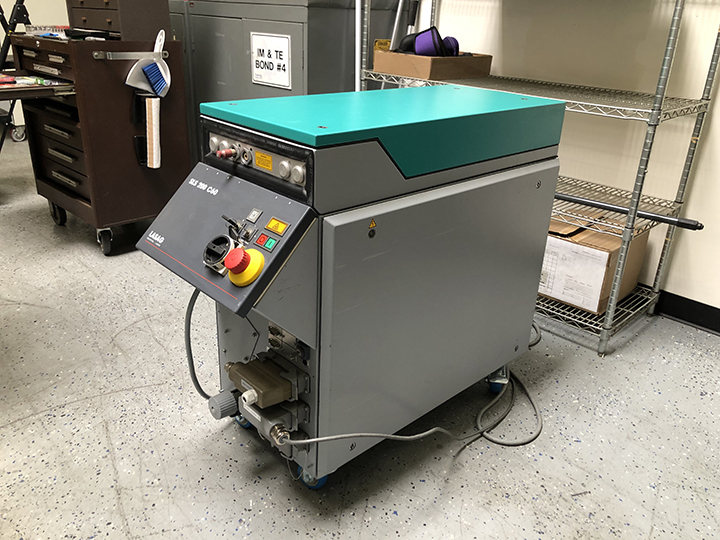
Our Laser Sources
We are using LASAG Laser-sources with outstanding capabilities and are able to shape the pulse of our beam to achieve high penetration without cracking materials. Our CTO has 30 plus years of hands-on experience, welding challenging materials.
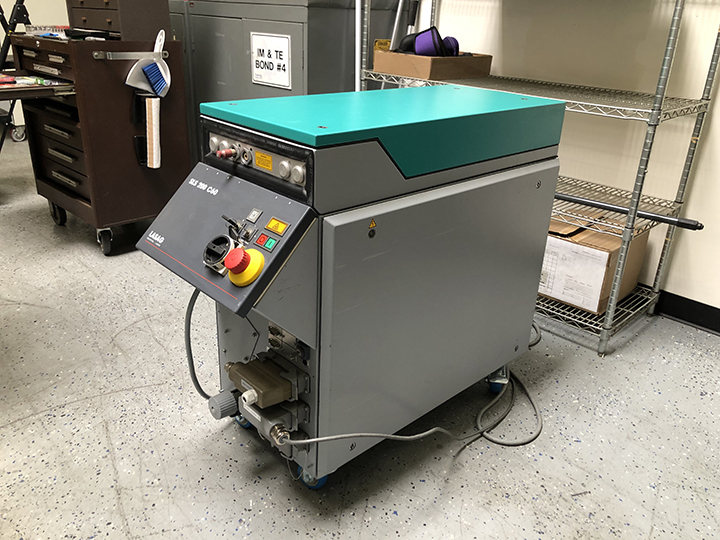
Our Laser Sources
We are using LASAG Laser-sources with outstanding capabilities and are able to shape the pulse of our beam to achieve high penetration without cracking materials. Our CTO has 30 plus years of hands-on experience, welding challenging materials.
Laser Welding
Laser welding provides precision joining of wires or plates and joining of metal components for finished assemblies and is a proven method for joining a wide variety of metals and metal alloys. Benefits include:
- Repeatable, high-speed and precise
- Ideal for high production volumes
- Minimum part distortion due to small heat affected zones
- Weldability near heat-sensitive components and hard-to-reach areas
- Consistent depth and width control
- Cost advantage
- Effective in dissimilar metal joining applications
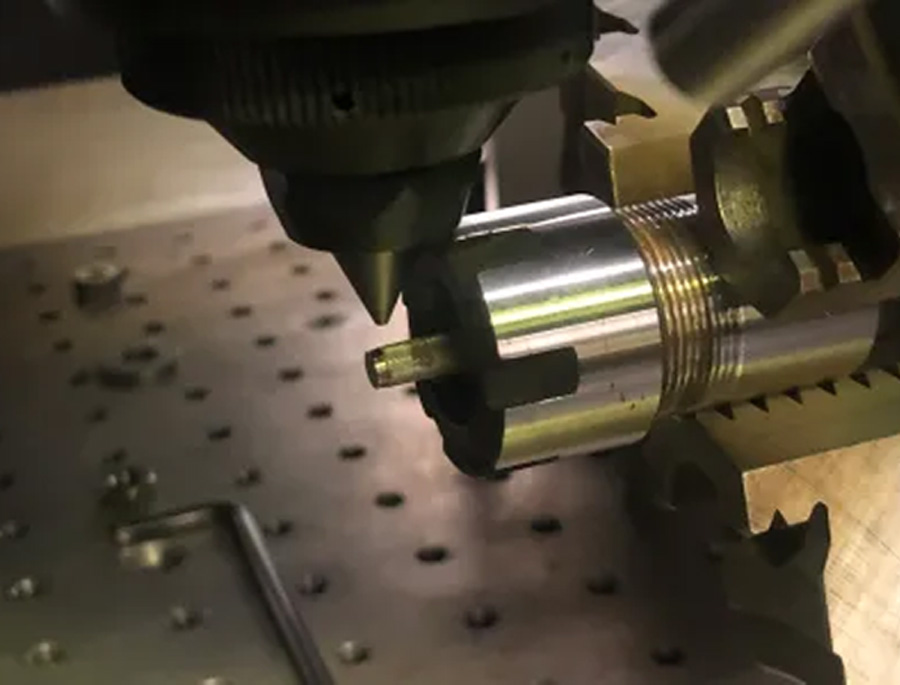
Laser Welding
Laser welding provides accurate, repeatable and reliable joining for critical devices and assemblies. At LASERONICS components are laser welded using a fixtured and automated system. Spot sizes as small as .0007″ diameter can be achieved with our advanced, automated circumferential weld.
Laser welding provides precision joining of wires or plates and joining of metal components for finished assemblies and is a proven method for joining a wide variety of metals and metal alloys. Benefits include:
- Repeatable, high-speed and precise
- Ideal for high production volumes
- Minimum part distortion due to small heat affected zones
- Weldability near heat-sensitive components and hard-to-reach areas
- Consistent depth and width control
- Cost advantage
- Effective in dissimilar metal joining applications
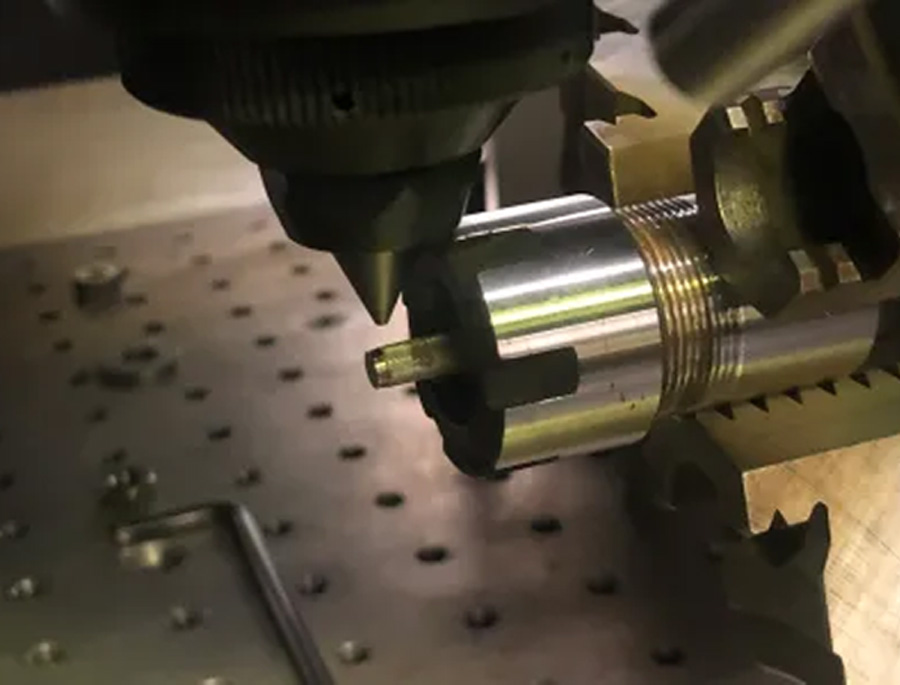
Laser welding is a process used to join metals or thermoplastics using a laser beam to form a weld.
Laser welding is increasingly used in industrial applications, because of the advantages it offers, such as high speed, high accuracy, low heat input and low distortion.
Being such a concentrated heat source, in thin materials laser welding can be carried out at high welding speeds of several feet per minute, and in thicker materials can produce narrow, deep welds between square-edged parts.
Laser micro welding on functional surfaces, for example, in medical engineering, aerospace/space and battery applications is gaining more and more importance. Our high-brilliance laser beam sources allow processing of parts in the micron range with a minimum of energy input.
Laser Beam Welding has numerous advantages over the voltaic arc heat source, such as narrower heat-affected zones, higher depth of penetration, lower deformation , single pass for the joining of thick plates , and higher welding speeds . Also, the use of our optical fibers to bring the laser beam to the weld joint enables our high degree of automation.
Laser welding can be very price competitive.
Key Advantages of Laser Welding
Clean Welds – In addition to the aesthetic benefits, clean laser welds yield significant safety and usability benefits. Clean welds allow for products that are easier to sterilize or fit into other assemblies without weld seam interference.
Strong Welds – Lasers provide high strength with a minimum number of welds, yielding time savings and increased reliability.
Hermetic Welds – Unlike soldering or brazing, lasers can provide flawless hermetic welds essential to many medical applications.
Excellent Repeatability – The laser’s output is incredibly stable, and with no electrodes to wear, bend or vaporize (and contaminate the weld nugget), weld repeatability is unmatched.
Easy Welding of Conductors – Materials such as Platinum, Gold, Copper alloys, Stainless Steel, Nitinol, Titanium, MP35N, Elgiloy and dissimilar metals can easily be welded with excellent results and repeatability.
Clean Process – Unlike soldering or brazing, lasers don’t need fluxes or solvents, keeping the work environment cleaner and safer.
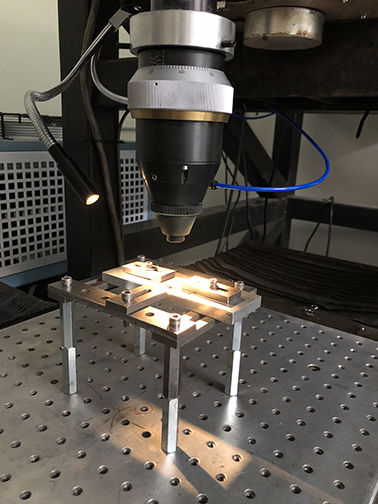
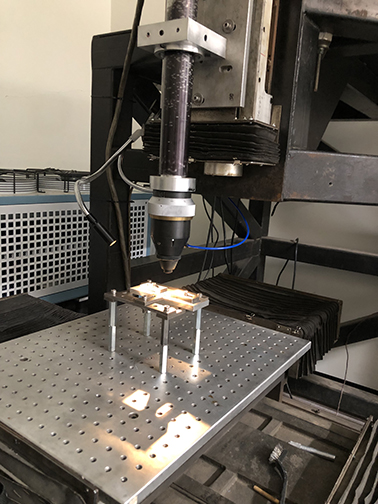
The peak power of a pulsed laser will overcome the reflectivity and heat conductivity of aluminum, copper, and other similar alloys. They can weld up to 3mm penetration. Peak power of around 1kW is needed for welding ferrous alloys and high nickel alloys. For aluminum alloys peak powers of about 3kW are needed and 5kW for copper alloys.
The temporal profile of the pulse can be “shaped” to optimize the weld quality and deal with dissimilar metals. Adjusting the peak power throughout the pulse will control cooling rates to reduce cracking, eliminate porosity, and improve weld esthetics.
Material-Combination Processed
Aluminum, Brass, Carbon steel, Cast iron, Coated steels, Copper, Hastelloy X , Inconel ,Molybdenum ,Monel, Nickel, Stainless steel, Tantalum, Titanium, Tungsten, Waspaloy, Zirconium
The peak power of a pulsed laser will overcome the reflectivity and heat conductivity of aluminum, copper, and other similar alloys. They can weld up to 3mm penetration. Peak power of around 1kW is needed for welding ferrous alloys and high nickel alloys. For aluminum alloys peak powers of about 3kW are needed and 5kW for copper alloys.
The temporal profile of the pulse can be “shaped” to optimize the weld quality and deal with dissimilar metals. Adjusting the peak power throughout the pulse will control cooling rates to reduce cracking, eliminate porosity, and improve weld esthetics.
Material-Combination Processed
Aluminum, Brass, Carbon steel, Cast iron, Coated steels, Copper, Hastelloy X , Inconel ,Molybdenum ,Monel, Nickel, Stainless steel, Tantalum, Titanium, Tungsten, Waspaloy, Zirconium

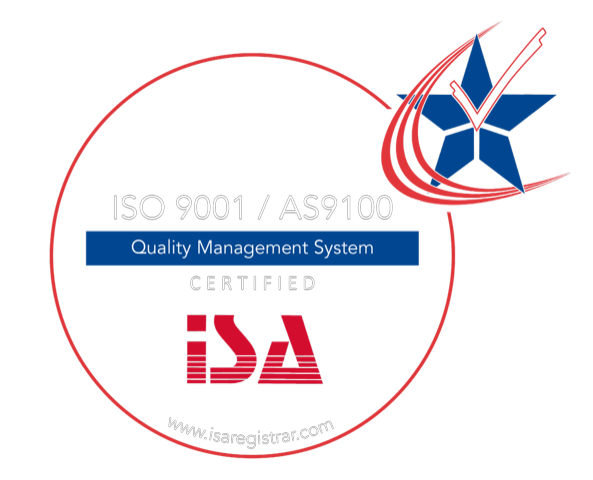
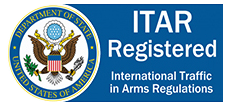

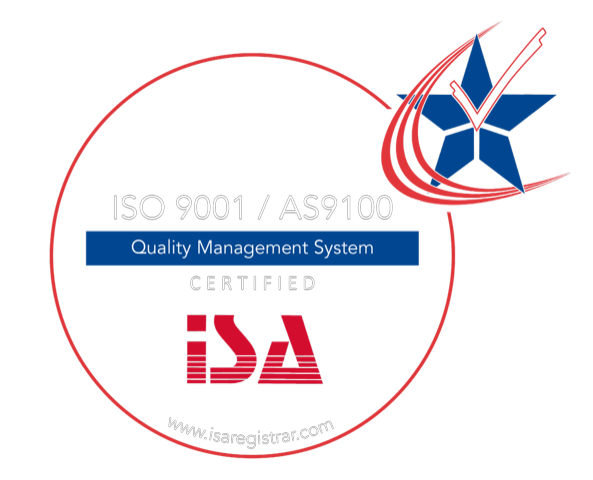
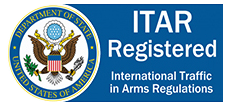
3667 San Gabriel River Parkway, Pico Rivera, California 90660, United States
Hours: Mon. – Fri. 7:00am – 6:00pm, Sat. 8:00am – 2:00pm • Sun. Closed